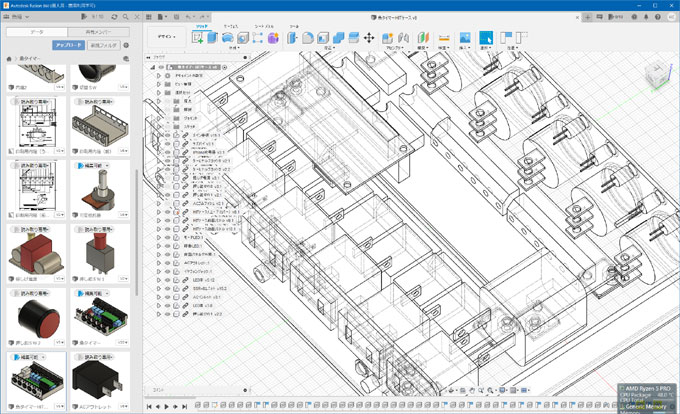
最近のフォトポタ電子工作部の様子。いったい何を・・・?
先日、格安ヒーターをインテリジェント化した、フォトポタ電子工作部。
次なる製品(?)として、サカナ・カメの水槽制御装置を作ろうと準備しております。
前回は図面もろくに書かずにやってしまって、最後のケース加工でてこずったため、今回はちゃんと、サラリーマンらしくパワポで描こうとしたのですが・・・。
真面目に図面を書こう!
今回作ろうとしているのは、我が家のリビングにある、サカナ水槽&カメ水槽の各種制御装置。
- 照明のタイマー制御
- エアーポンプのタイマー制御
- CO2添加装置のタイマー制御
- ヒーターの空焚き防止制御
- フィルターの空運転防止制御
- 冷却ファンの温度制御
こんなことを、ワンボードマイコン(Raspberry Pi)を中心に作ろうとしています。
回路図の方はそんなに難しくないので、簡単に手書きで描いてみました(実際は各種LED回路や運転切替SWなどが面倒ですが・・・)
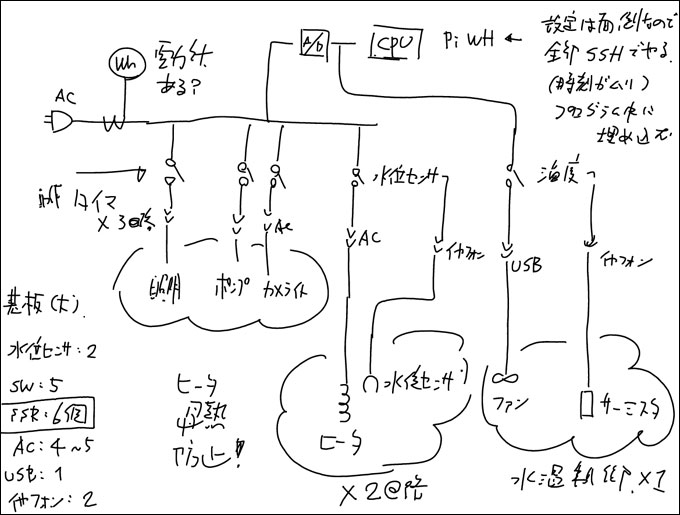
精密な回路図。完璧だ。
内蔵プログラムも数百行程度の短いもので簡単にできそうだし、後からどうにでも編集できるのですが、一番の難関は全体を収めるケースの作成。
前回は、図面もなしにアクリルケースに穴あけを行ったせいで、とても精度の低いモノができてしまい、いまだに心のトラウマになっております(オーバーな)
なので、今回は、まずはちゃんとしたケースを作るところ、いつもとは逆の手順から作ってみることにしました。
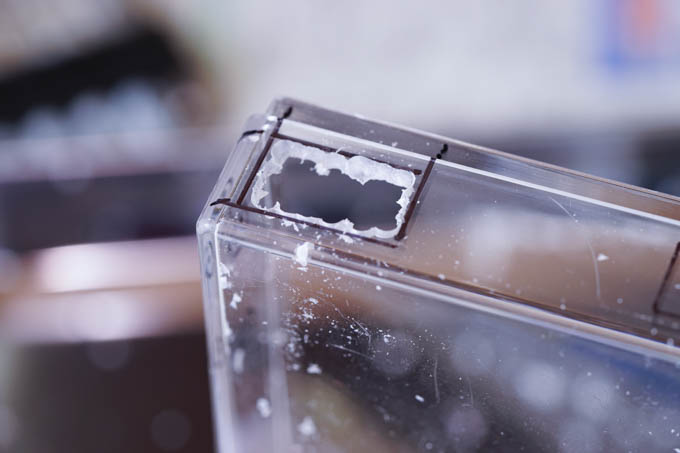
現物合わせで線引いて、適当な作業・・・。
SONY α7II + FE 90mm F2.8 MACRO G
真面目に図面を書こう!
使うケースは決まっていて、タカチというメーカーの「YM150」という、横150mm×高さ40mm×奥行90mmの小さなアルミケース。
この中に、結構多くの部品を押し込むことになります。
- マイコン(Raspberry Pi Zero)
- 操作スイッチ(自動・手動)×6個
- 動作表示LED×12個
- AC回路制御SSR×8個
- A/Dコンバータ、NORなどのゲートIC数個
- 各種センサー用コネクタ×4個
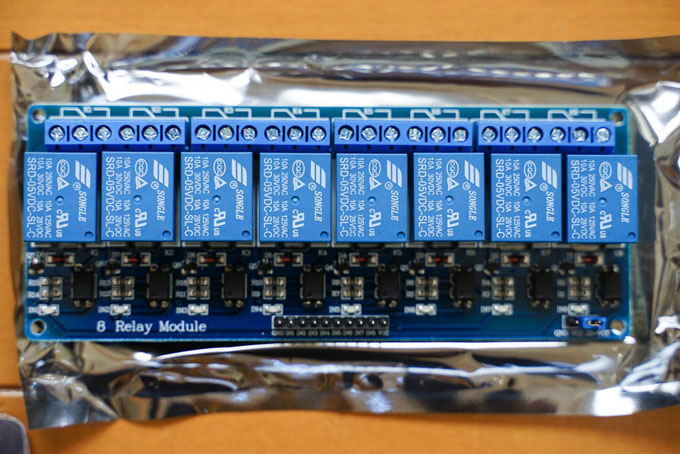
8回路のSSR(1000円)。これが結構でかくて、横幅140mmもある。
SONY α7II + FE 90mm F2.8 MACRO G
事前に試してみると結構な密度になりそうなので、一度、ちゃんと立体的に図面を描くことにしました。
と言ってもCADを使えるわけではないので、サラリーマンの秘密兵器、パワーポイントで描いてみました(いつもコレだ)。
レイヤーも採寸機能もないのに、ひたすらオートシェイプを並べ続けて描いたのがコレ。
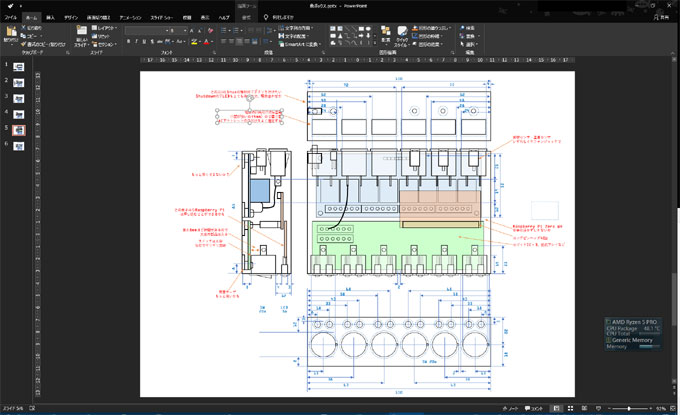
制御装置全体図。まさかのパワポで
寸法線の入れ方がいかにも素人っぽい(^^;
おぉ、いかにも「図面」っぽいよ!
まさか、これがパワーポイントで描いたとは、ビル・ゲイツもびっくりだと思います。
早速、この図面をもとにアルミケース加工を始めようとしたのですが・・・、致命的なミスが発覚!
ケースの横幅を150mmで描いていたのですが、よく考えたらこれは外寸であって、内寸は146mmしかないことが判明!
どび~ん、描き直しかよ・・・。
ド素人なのに、無理やり3D-CADに挑戦!
CADだったら、部品寸法が変わったらその数字を書き込むだけで、ちゃんと部品寸法が変わってくれると思います(使ったことないけど)
しかし、パワポでこんなに複雑にシェイプを書きまくった上にグループ化までやっている図に対して、「全体を4mm詰めてほしいんだよね」と言われても、どこをどうしたいいのか・・・。
途方に暮れること3日(うそ)、修正はあきらめて、CADで描いてみることにしました。
選んだのは、個人利用(やスタートアップ企業)では無償利用ができる、Autodesk社の「Fusion 360」。
初めて聞くCADですが、なんだか格好よさそうだし、なんたって無料ですから、これで行きましょう。
しかし、3Dどころか、2DのCADすら使ったことが無いわけですから、あまりにも独特なインターフェースが全く分かりません。
適当に箱や丸を書いて、適当にスイスイ~っと配置すればいいのかと思ったのですが、平面を選んで、部品を書いて、寸法を指定して、幾何拘束をかけて、3次元化して、ジョイントして・・・、めちゃくちゃに難しいです。
自転車の運転と、飛行機の運転くらい違います(おぉ、ちょうど2Dと3Dの乗り物だ)
しょうがないので入門書を買って、土日いっぱい勉強して(外走れよ・・・)、なんとか、所望する絵がおおよそ描けるようになってきました。
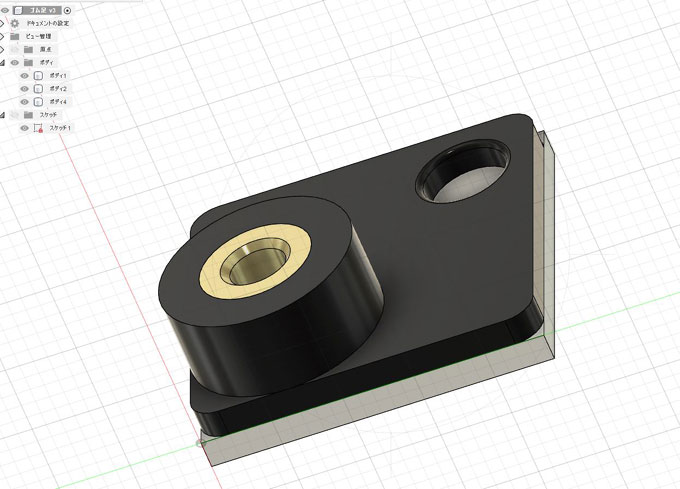
まずは、土台となるゴム足から。無駄に凝った作りにしてしまった・・・
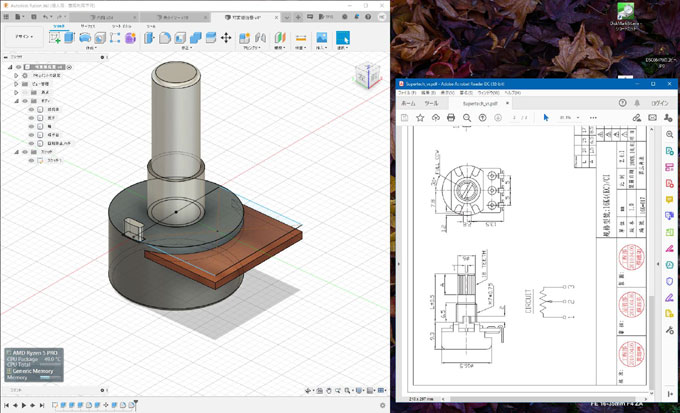
可変抵抗器メーカーの図面(→)から、3Dモデルを作る(←)
慣れてくると、これほど便利なものはないですね。
部品メーカーのデータシートで寸法を入手するか、自分でノギスで測るかして、使用予定の部品たちを3次元化していきます。
で、これらをケースの絵の中に押し込んでいくのですが、本当にモノを作る時のように、ケースに穴をあけて、そこの部品を嵌めこんで、という手順でやっていくのがとても楽しい(^^)
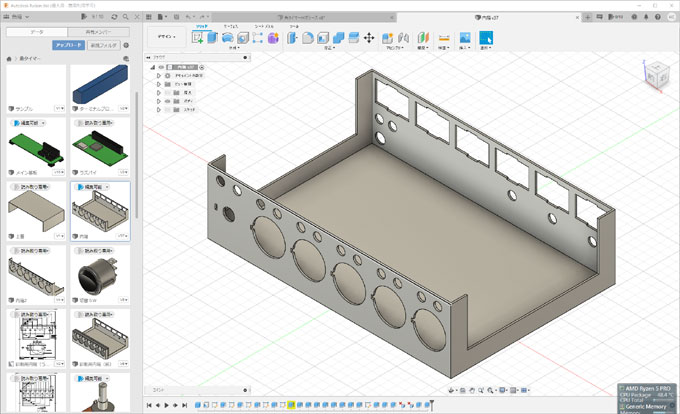
ケースの穴あけの状況。ここから採寸付きの図面も起こせる。
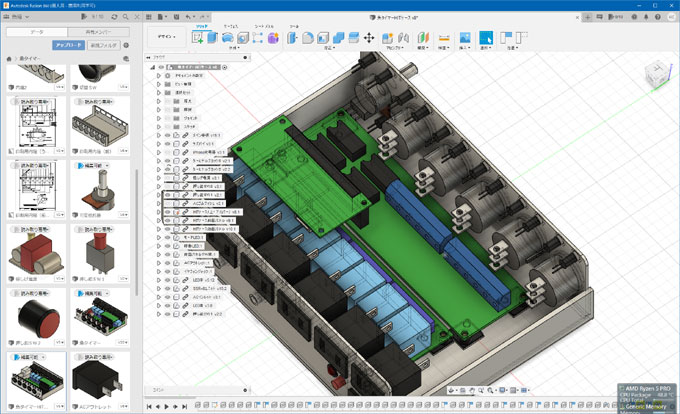
全部の部品を押し込んでみる。なんとか入りそう。
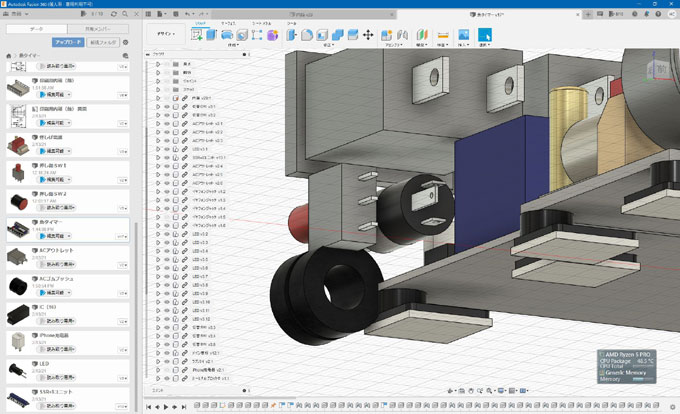
電源入力、出力、LED、リセットボタンなどがひしめく。クリアランスはぎりぎりか?
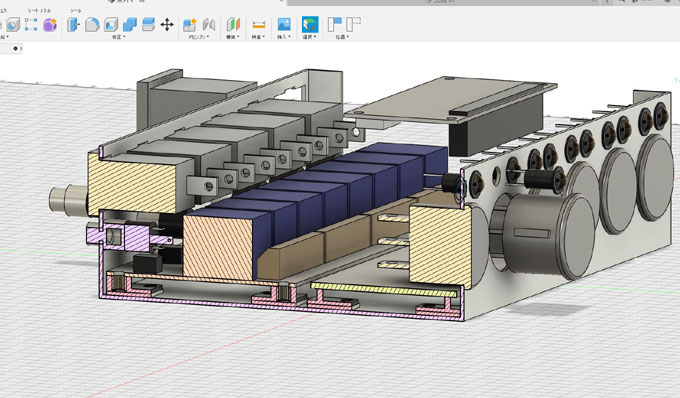
カットモデルも1クリックで。いや、3クリックくらいだったカモ。
出来上がった図は、3次元的にぐるぐる回したり、カットモデルも簡単にできるので、あらゆる部分で接触が無いことを事前に把握することができます。
あまりに楽しいので、「モノ作らなくてもいいや、図面だけで満足♪」と本末転倒になりかけるくらい面白いです(笑)
つづく
油断していたら、「DC電源ユニット」を内蔵することをすっかり忘れていました・・・。
しょうがないので、手元にあった、iPhoneの充電器(古き良き時代のやつ)を入れることにして、とりあえず作図してみました。
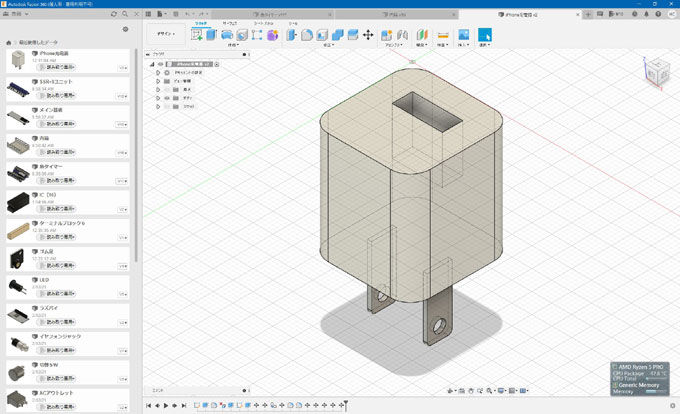
手元のiPhone充電器をノギスで測って再現。こんな感じ?
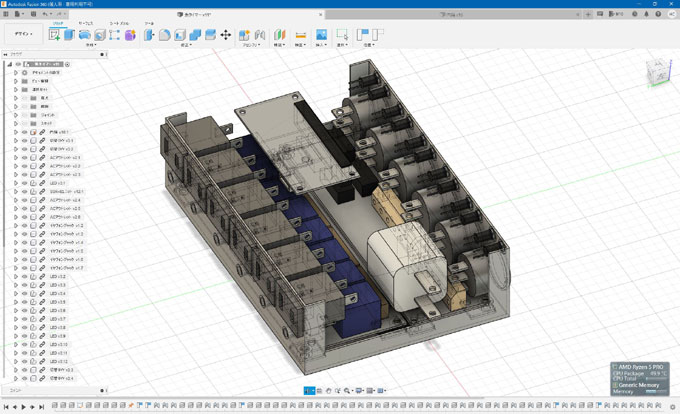
げっ、意外とデカい。もうちっと配置を練らねば。
が、予想以上に大きいんですね、iPhone充電器。
うまく入れられるよう、試行錯誤中です。あ~楽しい。
つづく・・・

3Dモデリングそのものが楽しくなる気持ちは良く分かります(笑
トライクには「普通の自転車用のライト」などの小物が「普通に」積めず、マウントをどうするか悩んで市販のマウントやアダプターを何段も重ねて使っていましたが、3Dプリントで標準のマウントを置き換える形で自作マウントを作ってスマートにマウント出来るようになりました。